ARCTURUS
MODERN SUBMARINE DESIGN
SEARCH: LIBRARY of CONGRESS SUBJECT HEADINGS
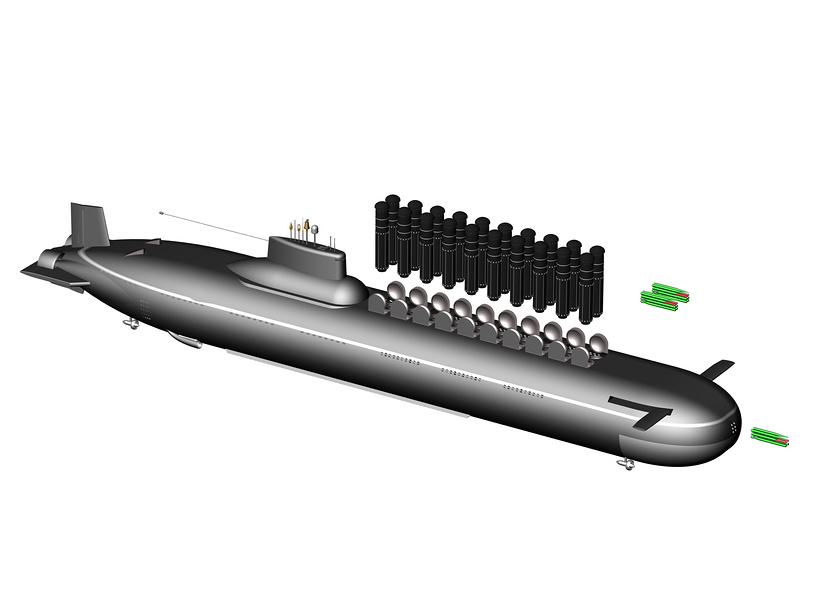
TECHNOLOGY - T
- Submarine - Types
- Submarine - Design
- Submarine - Warfare
- Submarine - Propulsion
- Submarine - Components
- Submarine - Nuclear Power
- Submarine - Fluid Dynamics
- Submarine - Solid Mechanics
- Submarine - Materials Sciences
- Submarine - Structural Analysis
- Submarine - Performance and Structure
- Submarine - Automatic Control and Guidance
- Submarine - Factory Architectural Design Plan
SUBJECT EXPERTS I
SUBJECT EXPERTS II
RESEARCH GUIDES
SUBMARINE NEWS
Program Development
Submarine design along with the construction processes must be well understood at both the macro/micro levels by the facility planning and engineering team(s) to ensure that an appropriate building concept is developed that is intergrated with manufacturing needs.
Design Aspects
The primary aspects of submarine design are: Propulsion, Controls, Mass, and Structure. The various design aspects are joined together into a coherent whole. All submarine design involve compromises of these factors to achieve the design mission.
Design Constraints
The design process starts with the submarines intended purpose. Research submarines are designed to observe ocean terrains while military submarines are are designed to perform surveillance along with providing support and warfare protection to logistical operatives.
Design Optimization
Modern research submarine and military submarine design projects are of such a large scale that every design aspect is supervised by different teams comprised of both engineers along with technicians and then amalgamated into a highly operable submersed vehicle which is able to function under diverse subterranean conditions.
Computer Designed Submarine
The design and engineering of submarines requires automated design. Computer languages allow electrical and mechanical engineers along with technicians to write programs using computer assisted design software structured to enhance efficiency and safety of deep water exploration and logistical maneuverability.
Design Process/Simulation
Submarine conceptual design involves forming a variety of possible configurations that meet the desired design specifications. The design process is maintained and regulated by adhering to both industry along with national standards. Structural configurations must satisfactorily meet all the requirements of the aformentioned design aspects .