ARCTURUS
MODERN AIRCRAFT DESIGN
SEARCH: LIBRARY of CONGRESS SUBJECT HEADINGS
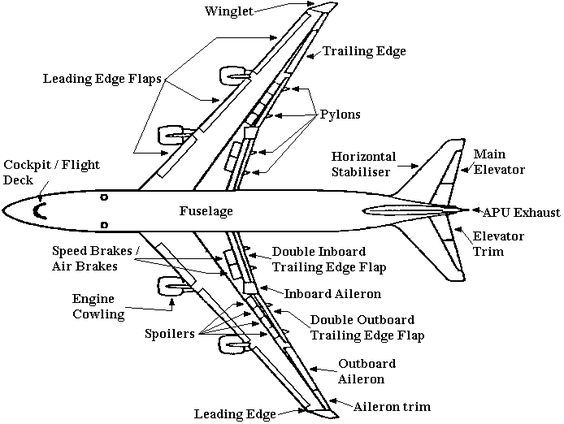
TECHNOLOGY - T
- Aircraft - Radar
- Aircraft - Engines
- Aircraft - Propulsion
- Aircraft - Hypersonic
- Aircraft - Conversion
- Aircraft - Fighter Jets
- Aircraft - Engineering
- Aircraft - Boeing 777X
- Aircraft - Facility Design
- Aircraft - Fluid Dynamics
- Aircraft - 777X Jet Engine
- Aircraft - Engineering 787
- Aircraft - Solid Mechanics
- Aircraft - Structural Design
- Aircraft - Materials Science
- Aircraft - Engineering GENX
- Aircraft - Structural Analysis
- Aircraft - Building and Assembly
- Aircraft - Performance and Structure
- Aircraft - Space Shuttle Structural Design
- Aircraft - Automatic Control and Guidance
- Aircraft - Factory Architectural Design Plan
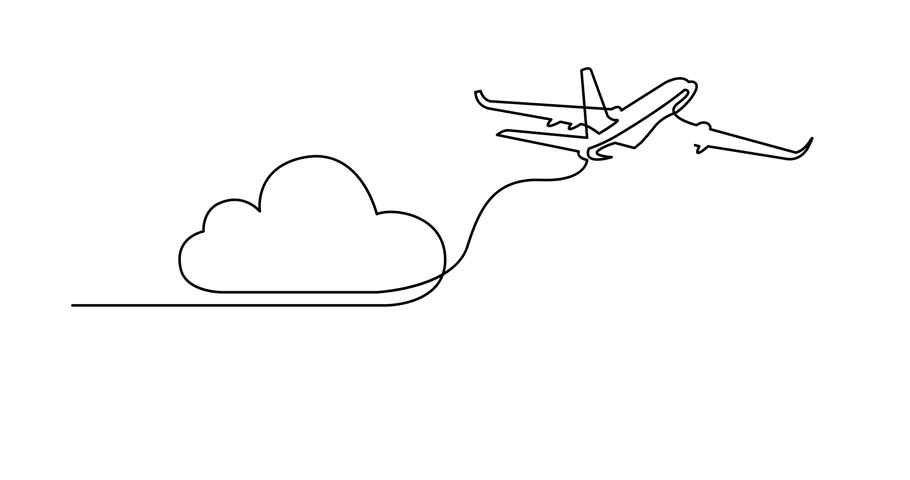
SUBJECT EXPERTS I
SUBJECT EXPERTS II
RESEARCH GUIDES
AVIATION NEWS
INTRODUCTION TO AERODYNAMICS (1)
INTRODUCTION TO AERODYNAMICS (2)
Program Development
The design/manufacturing process must be well understood at the macro level by the facility planning and engineering teams to ensure that an appropriate building concept is developed that is intergrated with manufacturing needs. Hiring a consultant(s) should be considered.
Design Aspects
The primary aspects of aircraft design are: Aerodynamics, Propulsion, Controls, Mass, and Structure. The various design aspects are joined together into a coherent whole. All aircraft design involves compromises of these factors to achieve the design mission.
Design Constraints
The design process starts with the aircrafts intended purpose. Commericial airliners are designed to transport passenger or cargo payloads, while fighter jets are are designed to perform high speed maneuvers along with providing support to logistical operatives.
Design Optimization
Commercial airliners and modern military aircraft design projects are of such a large scale that every design aspect is supervised by different teams comprised of both engineers along with technicians and then amalgamated into a highly operable transport vehicle which is able to function under diverse meterological conditions.
Computer Designed Aircraft
Computer languages allow aeronautical engineers to write programs designed to enhance safety and efficiency along with reducing workloads associated with many aspects of modern flight. Fly-by-Wire technology translates a pilots actions into electronic signals, which computers use to manipulate flight controls and landing gear.
Design Process/Simulation
Aeronautical conceptual design involves forming a variety of possible configurations that meet the desired design specifications. The design process is regulated by national airworthiness authorities. Structural configurations must satisfactorily meet all the requirements of the aformentioned design aspects.